A product capacity plan ensures you have enough products or ingredients for your deliverables For a florist, this would be flowers, vases, and cards For a pool maintenance company, this would be things like chlorine that are required to do the job Further, the key outcome of using a production capacity template excel spreadsheet is to keep the product inventory to a minimum level even fulfilling the customer demands So, good capacity planning for production results in a positive response to the fluctuation in product demand in different seasons over the product lifecycleFor example, a group of hospitals in a large urban area might agree that it is unnecessary for each to purchase expensive medical equipment for every ailment and that they ought to share capacity

Excel Based Resource Plan Template Free Download Project Management Templates
Level capacity plan example
Level capacity plan example-The purpose of this implementation plan is to outline a roadmap for the FDA's resource capacity planning (RCP) and modernized time reporting (MTR) capabilities pursuant to the agency'sPurpose of Capacity Plan Provide the purpose of the capacity plan For example Capacity planning is an important part of infrastructure and deployment planning A capacity plan supports the goal of optimum, and cost effective, provisioning of organizational resources and services by matching them to business demands



1
Capacity planning is a strategic process whereby a company determines what level of capacity it will need to satisfy the level of demand for To keep your capacity planning simple, you need to analyze your capacity plan at the team or skill level and not by analyzing individual resources Which means for example comparing how many project managers you need for yourHospital Capacity, Patient Flow, and Emergency Department Use in New Jersey i The Institute for Health, Health Care Policy and Aging Research Hospital Capacity, Patient Flow, and Emergency Department Use in New Jersey Derek DeLia, PhD A Report to the New Jersey Department of Health and Senior Services September 07 June 07
Selecting a capacity alternative most suited to achieving strategic mission 17 THREE STEPS OF CAPACITY PLANNING 18 Determine Service Level Requirements 19 The first step on the capacity planning process is to categorize the work done by systems and to quantify users' expectation for how the work gets down Define workloads 21Figure shows the level capacity plan of a company manufacturing a product on produce to stock and sell basis In the first quarter aggregate demand is less than production and inventory builds up till the end of the First Quarters in the second third and fourth quarters are inventory levels Decline because production is less than the aggregate demandThe steps are in order Evaporation, Wash, Centrifugation, Grinding, Drying, Sack, Packaging, Shipping
Generally, these options fall into two "pure strategies" – a chase strategy and a level strategy Under the chase strategy, production is varied as demand varies With the level strategy, production remains at a constant level in spite of demand variations (00) LEVEL STRATEGY FOR CAPACITY PLANNING In Swamidass PM (edsSlack, Chambers and Johnston, 08) Identified capacity strategies are the 'level' capacity strategy with a uniform output level;Level gauges and were constructed in accordance with UL 142 The 1,0 has a capacity of less than 55 gallons (such as the 25gallon containers of adjuvant oils, quart containers of turpentine, gallon containers of mineral spirit, and 5gallon gas cans) sample plan • • • • •
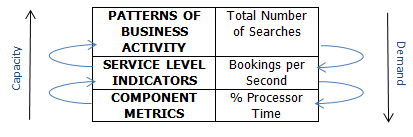



3 Level Capacity Management Case Study



1
What is a level capacity plan? An approach to aggregate planning that attempts to match supply and output with fluctuating demand Depending on the product or service involved, the approach can incur costs by the ineffective use of capacity at periods of low demand, by the need to recruit or lay off staff, by learningcurve effects, and by a possible loss of quality The advantages include low storageThe idea here is that a level schedule is used during consistent periods and the chase strategy is used during months with fluctuating demand This can be helpful in seasonal business For example, a company that made Halloween chocolates, may maintain a level schedule for 9 months of the year and then use a chase strategy during the weeks
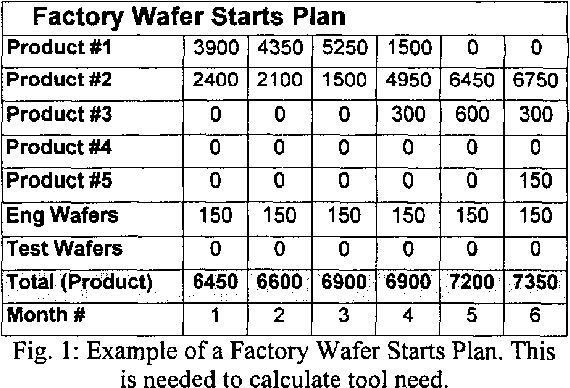



Capacity Planning Model The Important Inputs Formulas And Benefits Semantic Scholar
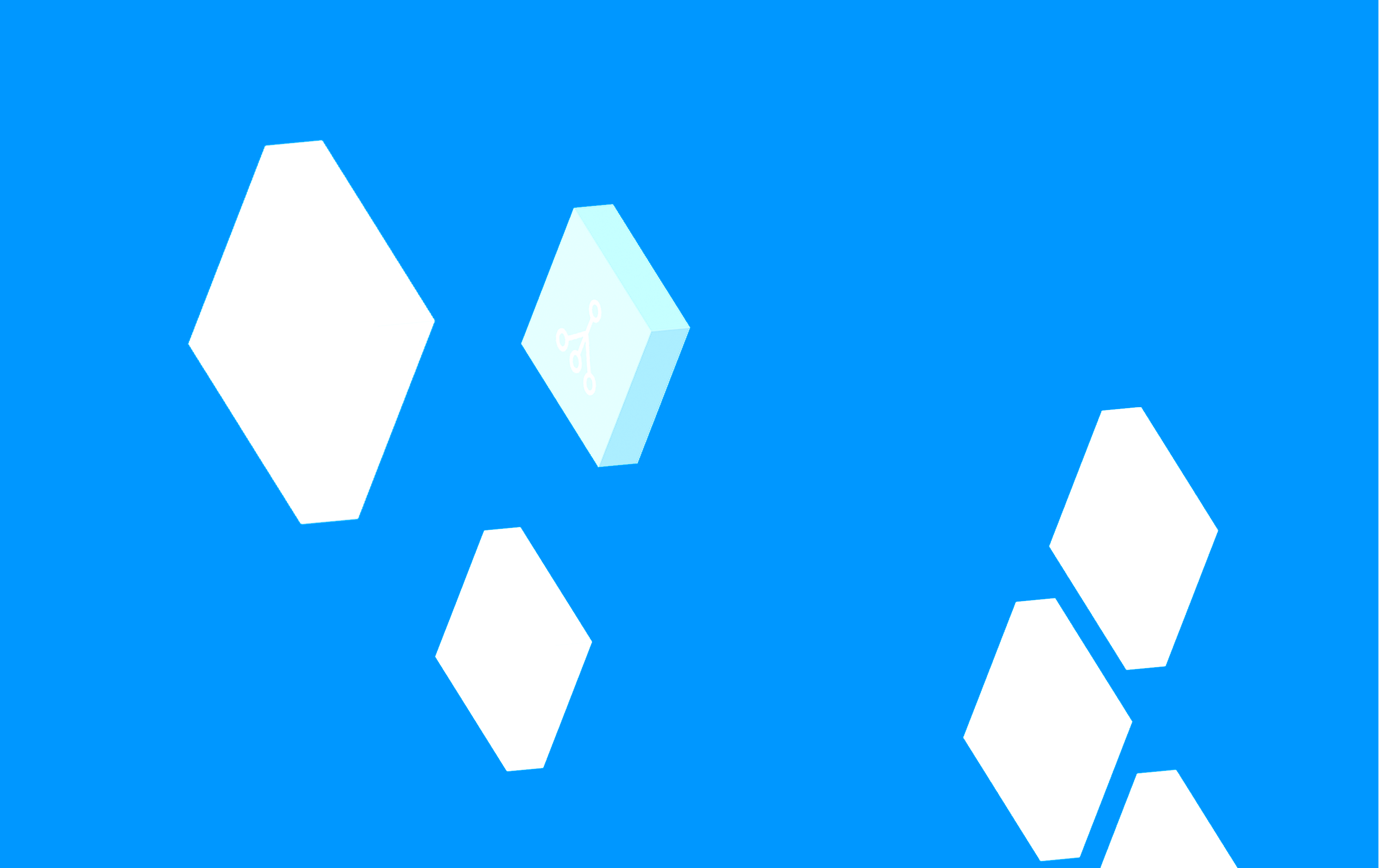



Workclout 3 Case Studies Examples Of Capacity Planning
Business capacity is the volume of work that can be handled by an organization, team, process, service or tool It can often be scaled up and down by adding, reallocating and subtracting resources The following are illustrative examples of a business capacityAn example of level capacity management could be the first step of the production of salt by evaporation (in Italy there is one industry like this in Salina) In hot countries, salt is produced by allowing the sun to evaporate sea water in shallow pools or 'pans';Capacity utilization is the proportion of available capacity that is utilized and is quantified by the ratio of actual output to capacity output (Nelson, 00;




Capacity Planning What Is It And How Do I Implement It Projectmanager Com
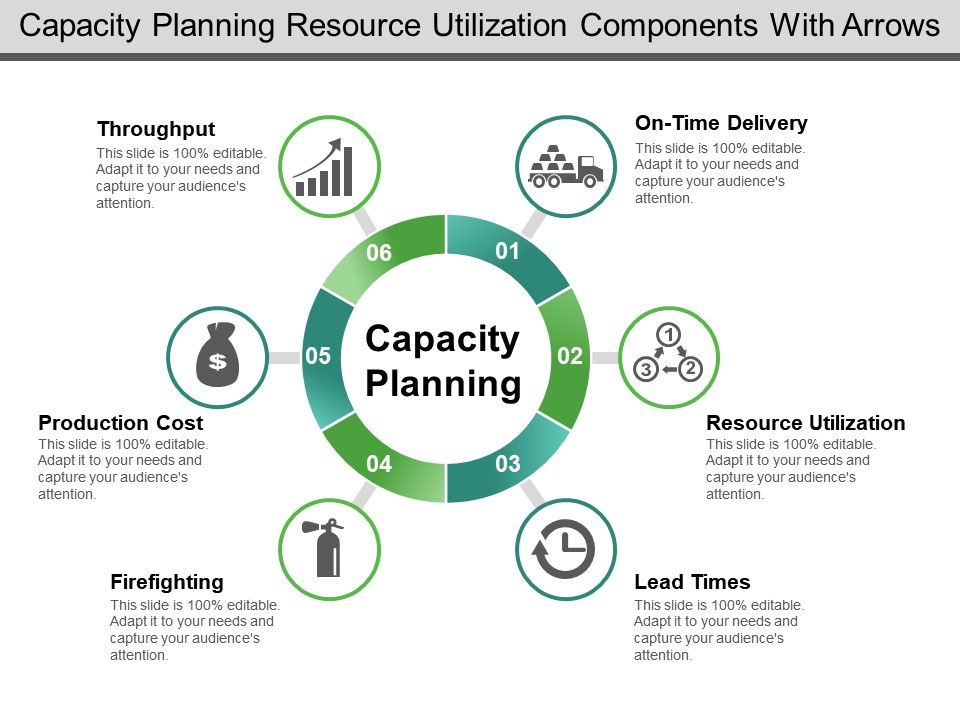



Capacity Planning Resource Utilization Components With Arrows Powerpoint Slides Diagrams Themes For Ppt Presentations Graphic Ideas
Production, Capacity and Material Planning a Production plan `quantities of final product, subassemblies, parts needed at distinct points in time a To generate the Production plan we need `endproduct demand forecasts `Master production schedule a Master production schedule (MPS) `delivery plan for the manufacturing organization– Sets labor/equipment capacity to satisfy period demands – Disadvantage constantly changing short term capacity ERPDOM (Spring 16) 6 Level Plan Example • Level production rate= 28,000 units/7 periods= 4000 unitsAnd the 'chase' capacity




Capacity Planning Template Explore 7 Tips For Effective Planning Project Management Templates




Set Sprint Capacity Azure Boards Microsoft Docs
Simply put, if capacity is the means to plan and achieve, then capacity development describes the ways to those means An essential ingredient in the UNDP capacity development approach is transformation For an activity to meet the standard of capacity development as practiced and promoted by UNDP, it must bring about transformation that is Capacity Planning It's pprove/cancel projectsCapacity requirement planning forms part of the operational stage of the planning process and works in conjunction with a manufacturing requirement planning (MRP) system A detailed capacity requirement plan provides an operational level overview for the production cell and assists the operations manager with identifying all of the elements




How To Do Capacity Planning Youtube
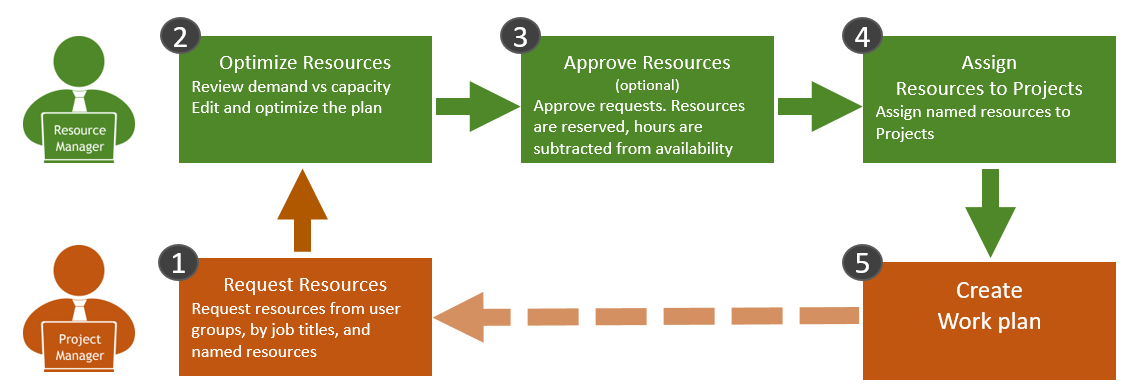



Capacity Planning Everything You Need To Know Opensense Labs
1 The utilization of operational resources throughout the year 2 Efficient level of production can be maintained 3 Decreases the marginal cost The disadvantages of the level capacity strategy include 1 If there is any change in the demand of the customer there is a risk of obsolescenceCapacity Plan Template Version Xx This Capacity Plan is an integral part of infrastructure and deployment planning It supports the goal of Service Level Agreements (SLAs), utilization reports, capacity modeling, and workload forecasts9 HighLevel Project Plan Examples – PDF Highlevel planning is focusing on establishing your project's requirements and deliverables, and then tracking them over time Every time you estimate a new project and assign resources to it, you are actually creating a highlevel project plan
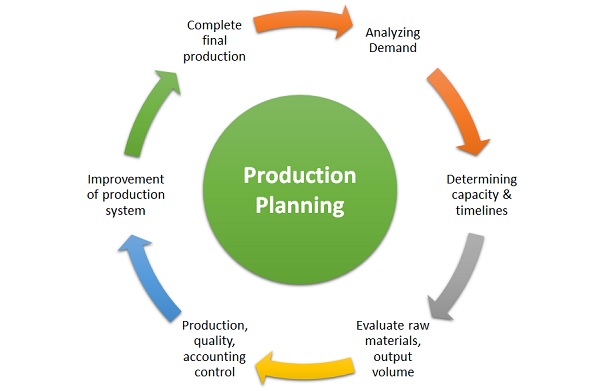



Production Planning Meaning Importance Steps Example Mba Skool




Capacity Planning Everything You Need To Know Clicktime
Resource level Capacity vs Demand Clearly two resources Developer 3 and Developer 2 do not have enough capacity to complete the tasks assigned to them Meanwhile, 3 other resources have a lot of additional hours available but not utilized In the next page of the dashboard, you can see the charts of Capacity vs Demand in HoursThe Capacity Plan is used to manage the resources required to deliver IT services The plan contains scenarios for different predictions of business demand, and options with cost estimates to deliver the agreed service level targets Prologue to Capacity Management and Availability Management (CAM) The capacity and Availability management field involves setting up and oversight of capacity and availability at a reasonable cost with proficient utilization of resources Various levels perform this process in an organization across allied services Download This Template It includes and serves



Capacity Plan Template Technical Writing Tools
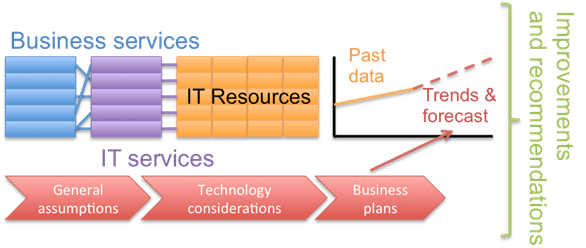



Itil Service Design Itil Capacity Plan
3 Examples of Production Capacity John Spacey, Production capacity is the volume of products or services that can be delivered by the operational resources of an organization Resources include factors such as land, labor, facilities, infrastructure and machines The following are illustrative examples of production capacityExplain about the level capacity strategy Level capacity strategy The organisation produces or manufactures at a constant rate of output avoiding any changes or fluctuations within customer demand levels This frequently implies stockpiling or higher holdings of inventory while customer demand levels reduceUse break even analysis to evaluate capacity alternatives This module examines how important strategic capacity planning is for products and services The overall objective of strategic capacity planning is to reach an optimal level where production capabilities meet demand Capacity needs include equipment, space, and employee skills




Top 12 Resource Management Best Practices Planview
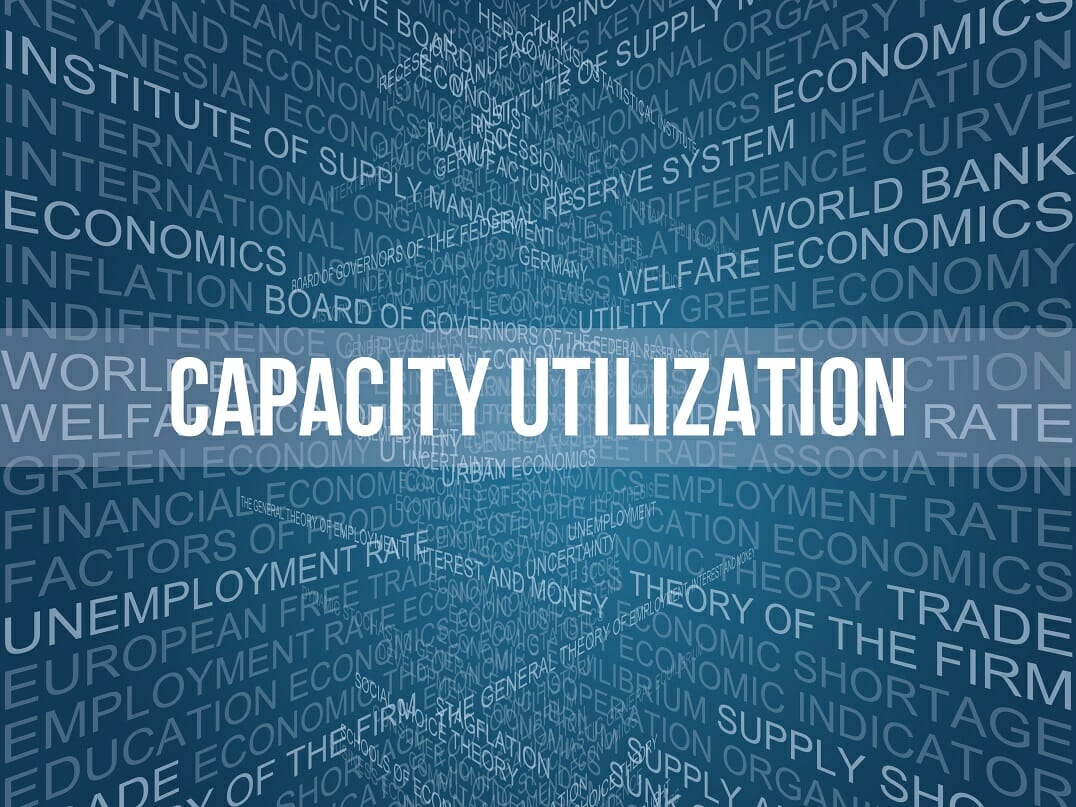



Capacity Utilization Definition Example And Economic Significance
A period's planned quantity of output is equal to that period's expected demand Level capacity strategy When an organization adopts the level capacity strategy then it manufactures at a constant output rate It does not consider any fluctuation or change in the level of demandConcept of Capacity Planning It means the optimum level of output that can be gotten within a specified period It means the optimum level of output, given the changes in product mix, equipment maintenance, programming and operating issues, labor problems, etc It usually is less than the total design capacity1 Capacity Development Working Group (WG) Terms of Reference (June 10) 2 Organizational Capacity Assessment Sheet (version 2) 3 Individual Capacity Assessment Sheet (version 1 and version 2) 4 Sample of Programme Design Matrix (PDM) 5 Sample of Plan of Operation (PO) 6 Evaluation Sheet for final Presentation
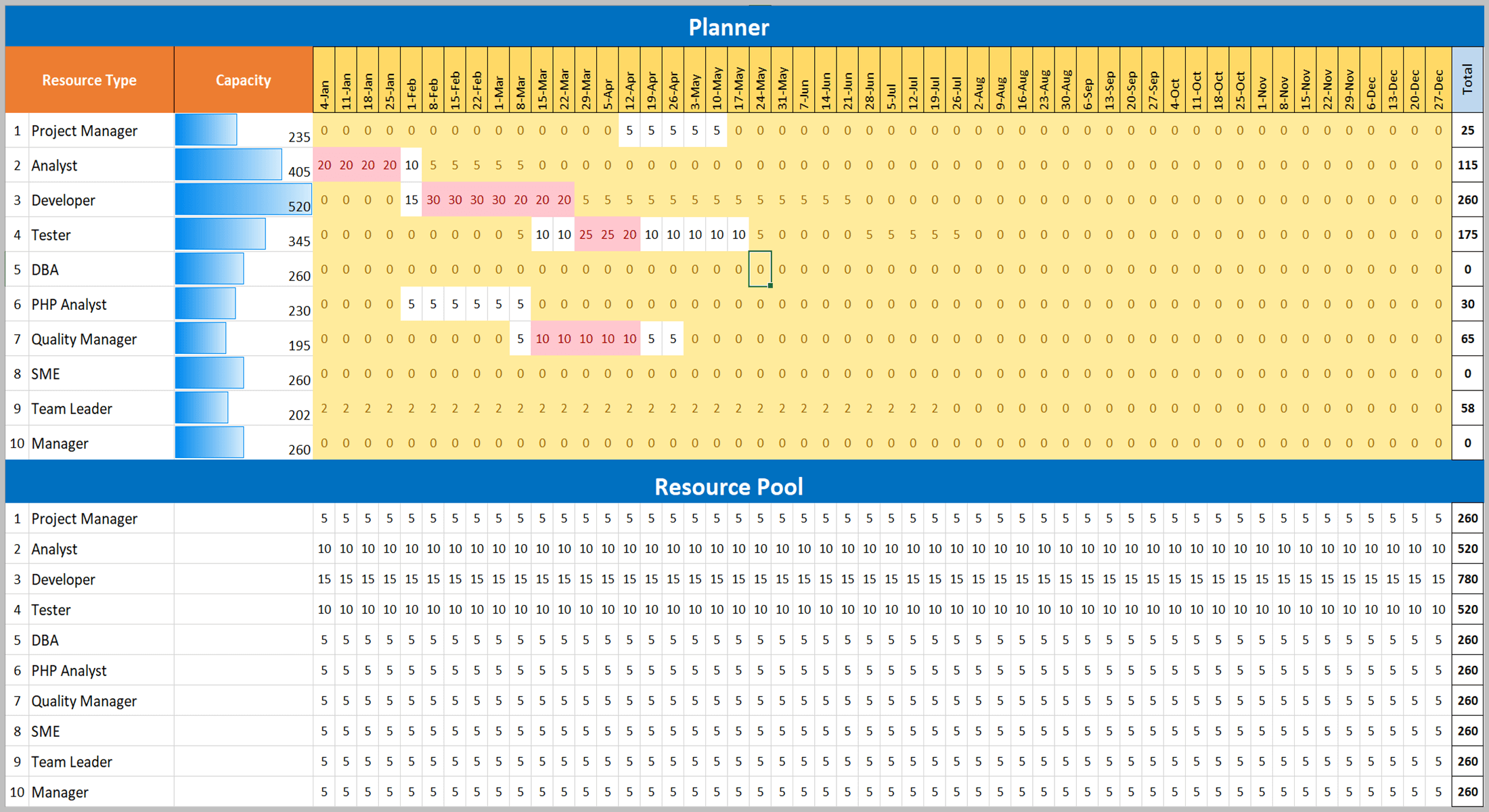



Excel Based Resource Plan Template Free Download Project Management Templates
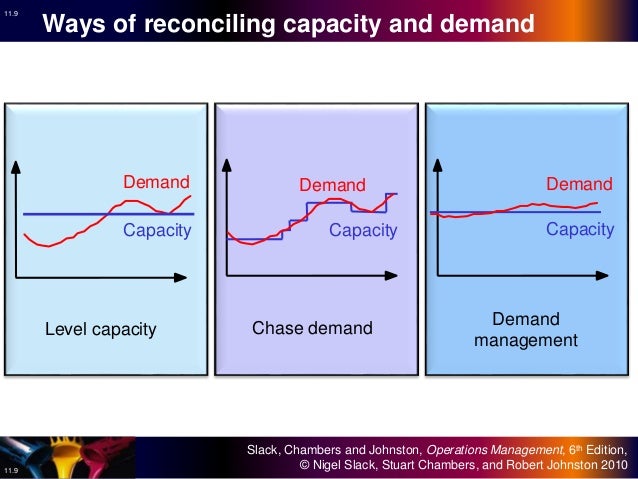



11 Capacity Planning And Control Operations Management
UPMC St Margaret Hospital Surge Response Plan 3 LEVEL DEFINITION AND CRITERIA NEDOCS Score and Interpretation LEVEL 1 – 2 NEDOCS = 0 – 60 Not busy busy LEVEL 3 NEDOCS = 61 – 100 Extremely Busy, not overcrowded LEVEL 4 NEDOCS = 101 140 Overcrowded LEVEL 5 NEDOCS = 141 – 180 Extremely Overcrowded Level 6 NEDOCS = 181 – 0Steps Entering the production data We will then determine the hire/fire rate to get to production level that is desired All inventory levels will then be updated We will also check whether the inventory is going to run out – If it does recalculate average production needed and go to step 1 Calculate totals for each category Calculate costsCapacity is often measured in hours available to be worked by employees And in this context, "planning" is the act of scheduling employee hours against a fixed or expected amount of work Example A company has 10 employees Each employee works 40
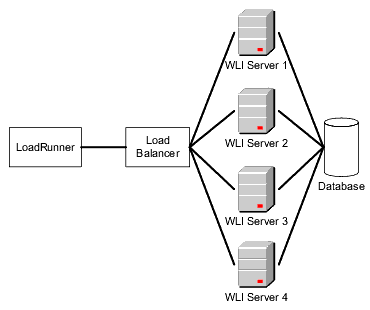



Capacity Planning Example




Capacity Plan Template Word Templates For Free Download
Figuring out the ideal time to start production can be a headache when managing your shop floor But you can cure those aches by adopting capacity planning into your business, a model that's going to help you determine the most realistic approach to manufacturing In this article, we look into what is resource capacity planning, how it works, and how you can getSample Capacity Building Plan DRAFT Rev 10 4 Guiding Principles During the Change It is important for Organization ABC personnel to follow these principles as it implements the actions in this Plan 1 Focus on what is needed to change, not on the way it has always been done before 2 Strategies The broad classes of capacity planning are lead strategy, lag strategy, match strategy, and adjustment strategy Lead strategy is adding capacity in anticipation of an increase in demand Lead strategy is an aggressive strategy with the goal of luring customers away from the company's competitors by improving the service level and reducing lead time
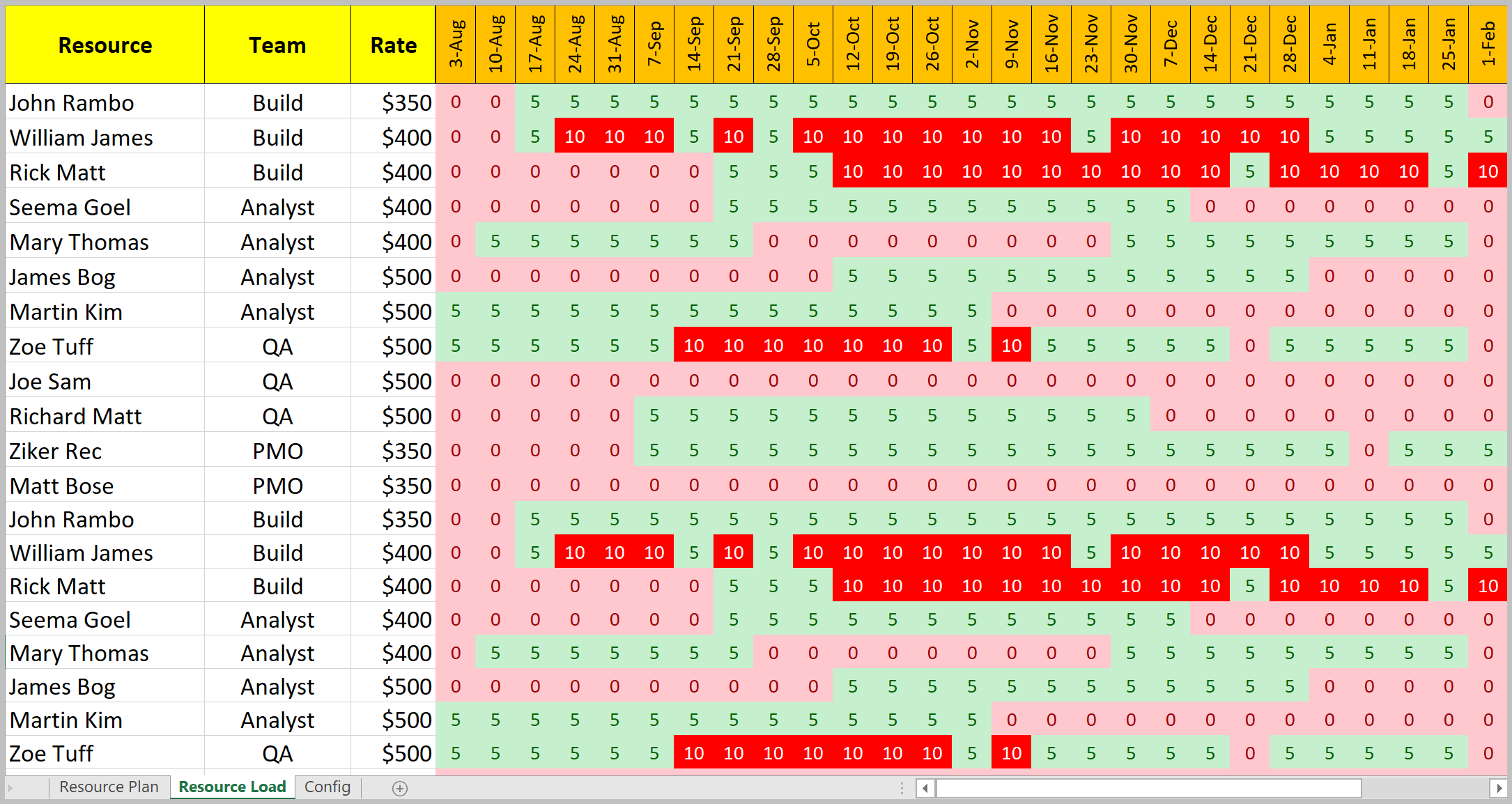



Excel Based Resource Plan Template Free Download Project Management Templates




Capacity Plan Template Ms Office Templates Forms Checklists For Ms Office And Apple Iwork




Capacity Management It Process Wiki



1




Capacity Planning An Overview Sciencedirect Topics




Capacity Planning In Project Management 4 Vital Success Factors Update 21
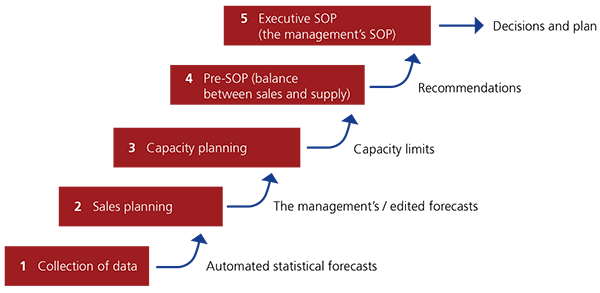



Sales And Operations Planning Relex Solutions



Capacity Planning 3 Methods How To Implement Them Optimoroute



3
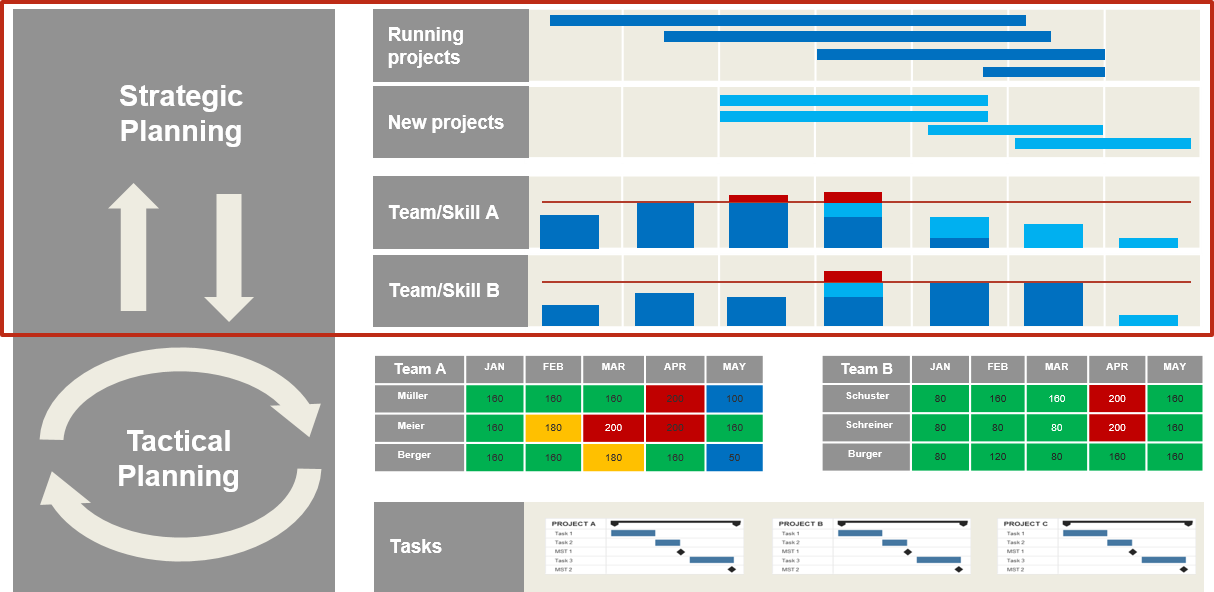



Capacity Planning Everything You Need To Know Opensense Labs




Match Supply And Demand In Service Industries
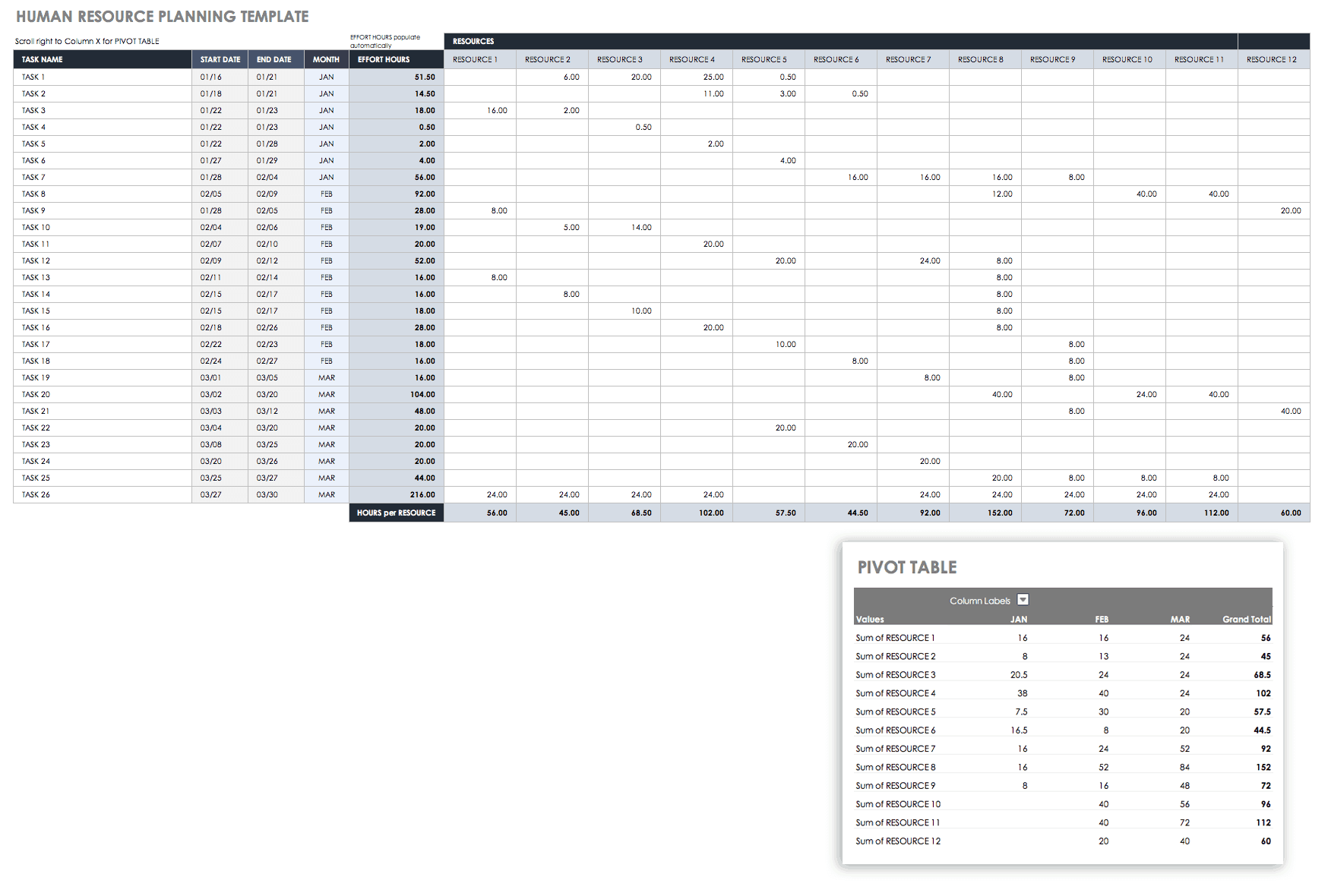



Free Resource Planning Templates Smartsheet
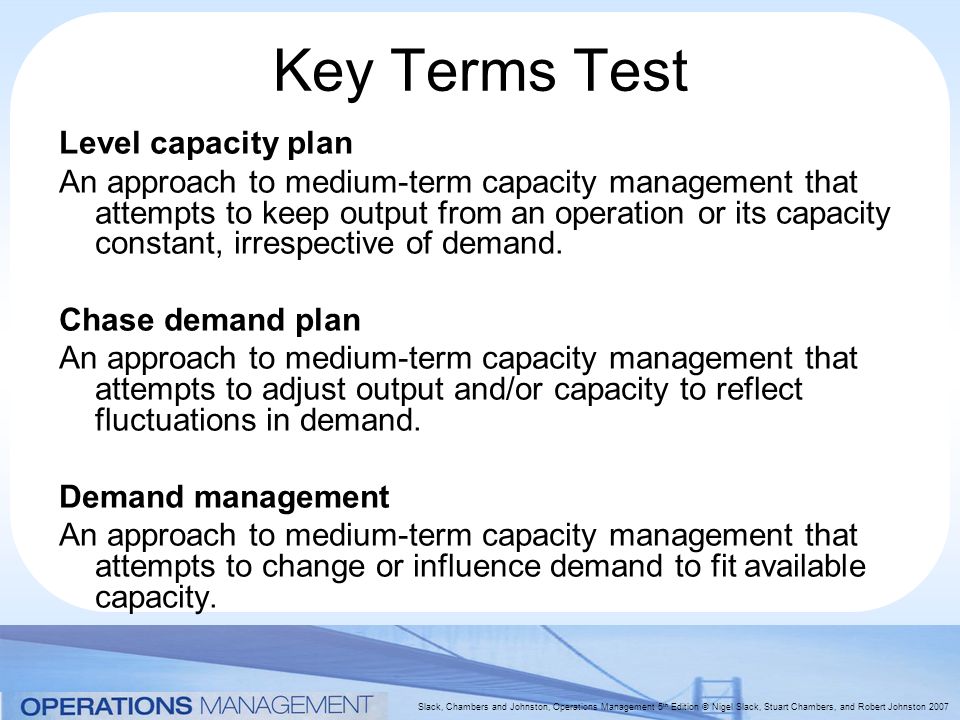



Capacity Planning And Control Ppt Video Online Download
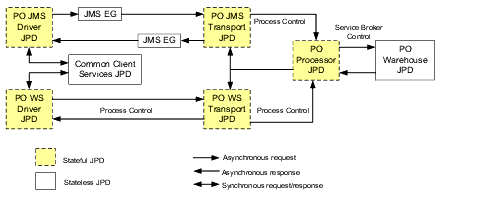



Capacity Planning Example
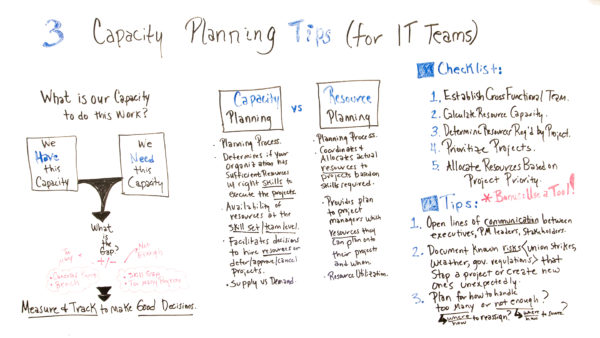



Capacity Planning What Is It And How Do I Implement It Projectmanager Com
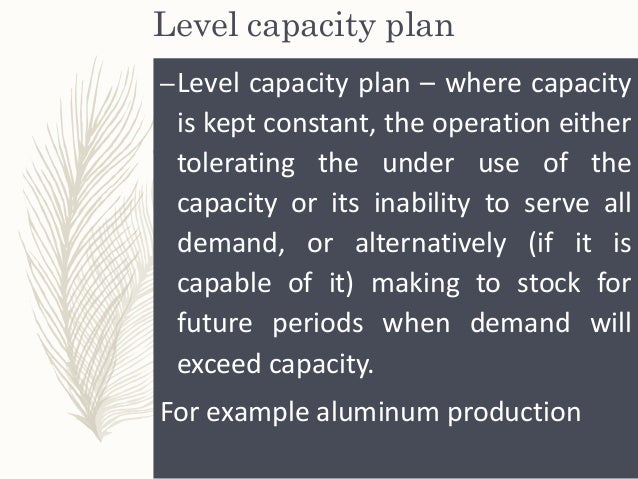



Capacity Planning And Control
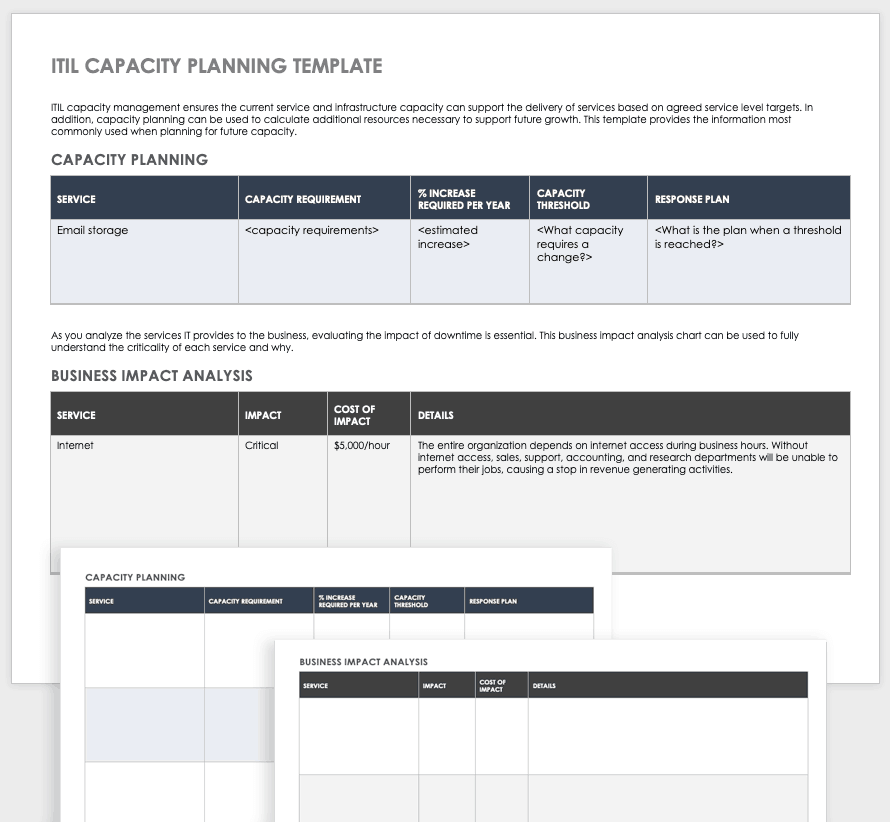



Free Itil Templates Smartsheet




Capacity Building Wikipedia
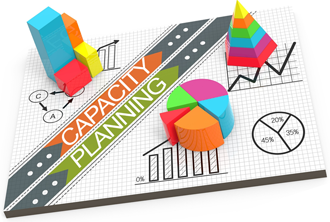



Capacity Planning Meaning Classification And Its Goals
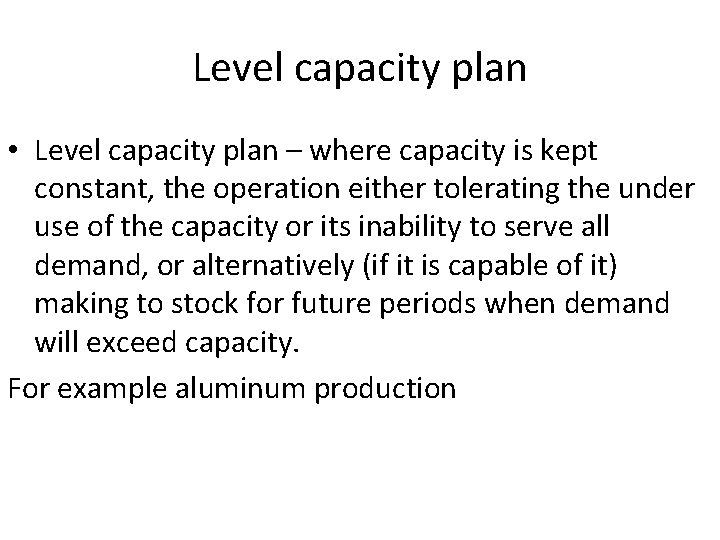



Capacity Planning And Control Chapter 11 What Is




Excel Based Resource Plan Template Free Download Project Management Templates
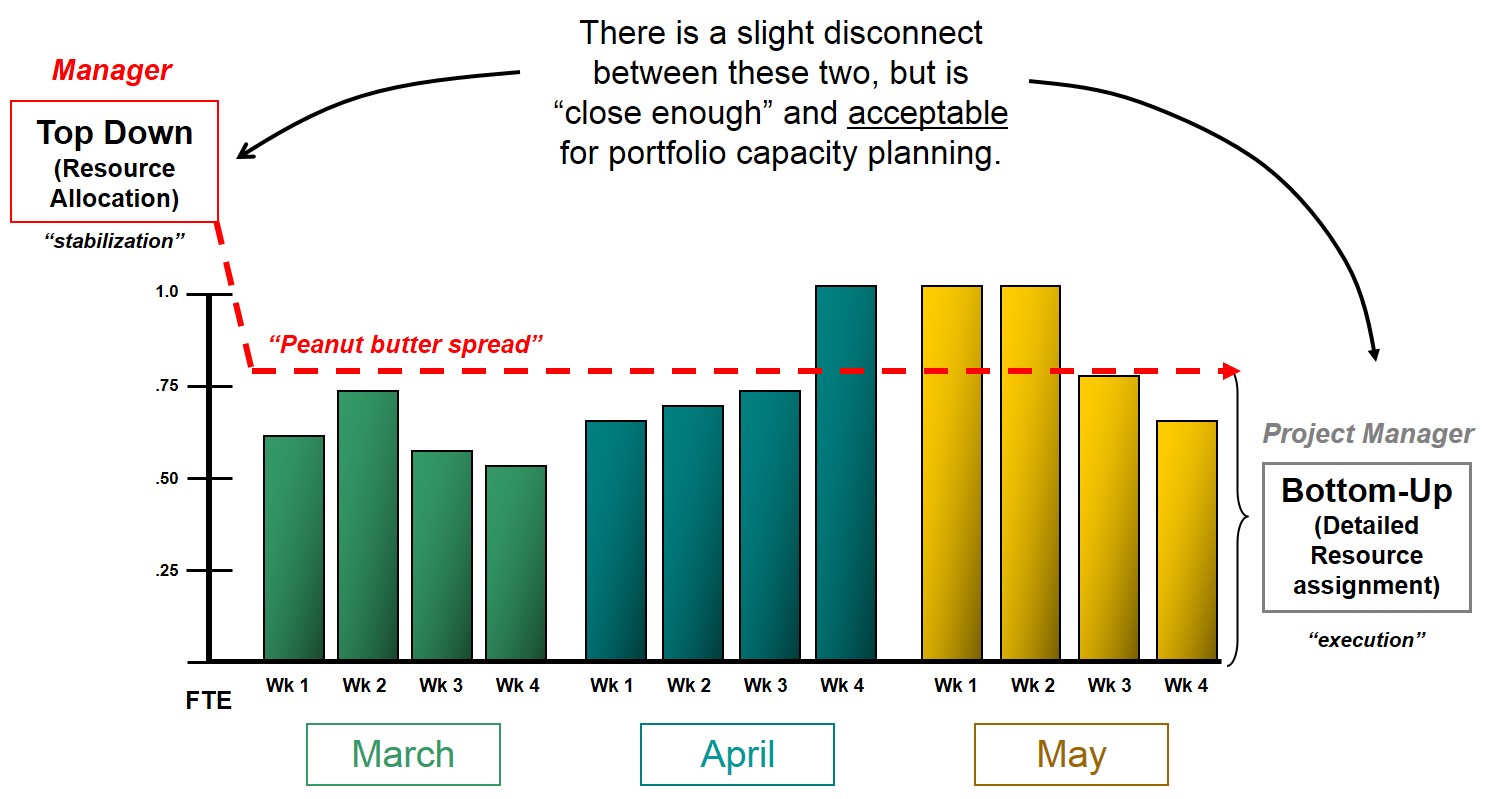



The Goal Of Resource Capacity Management
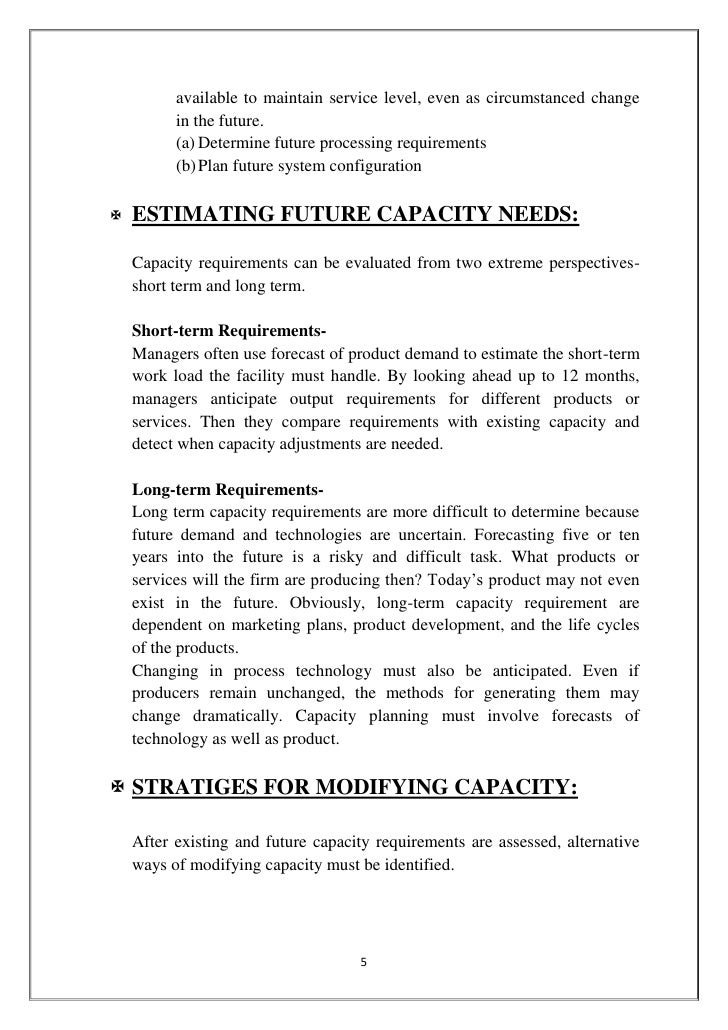



Capacity Planning




Chapter 3 Strategic Capacity Management Ppt Video Online Download




Capacity Planning Everything You Need To Know Clicktime




How To Calculate Production Capacity Of A Factory



How To Do Effective Capacity Planning On The Scrum Team
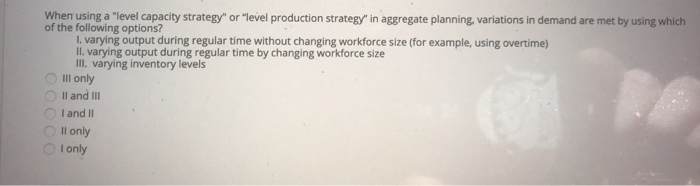



When Using A Level Capacity Strategy Or Level Chegg Com




Manage Resource Capacity Planning Scenarios




Entries For Thursday 25 October 07 Sergio S Blog
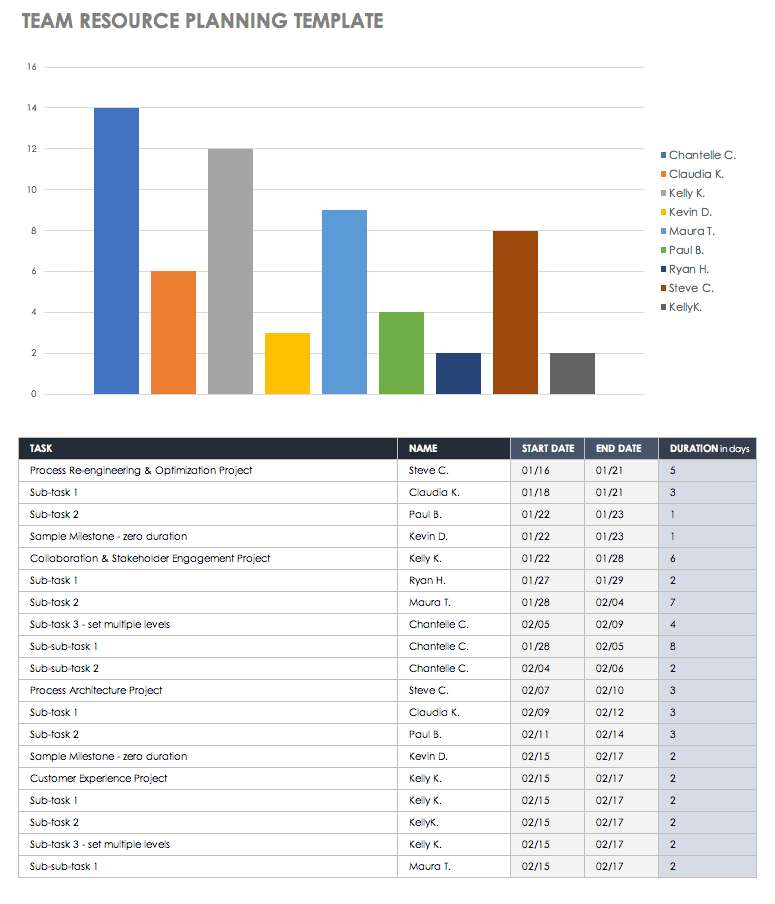



Free Resource Planning Templates Smartsheet




Iteration Planning Scaled Agile Framework




Capacity Planning 3 Methods How To Implement Them Optimoroute
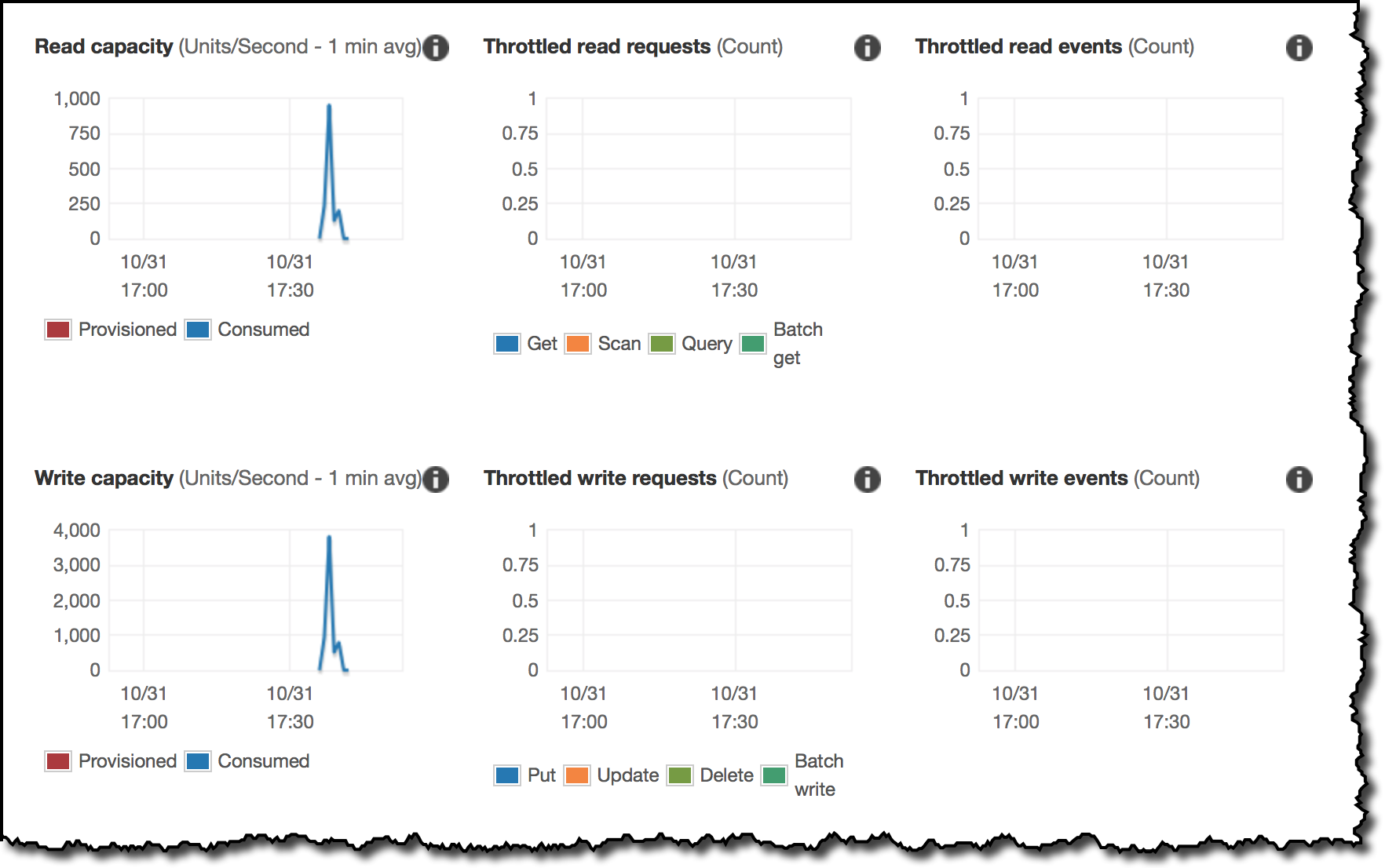



Amazon Dynamodb On Demand No Capacity Planning And Pay Per Request Pricing Aws News Blog




26 Resource Capacity Plan Template Resource Planning Template Human Capacity Project In 21 Action Plan Template Business Letter Template Business Plan Template Free



Capacity Plan Template Technical Writing Tools
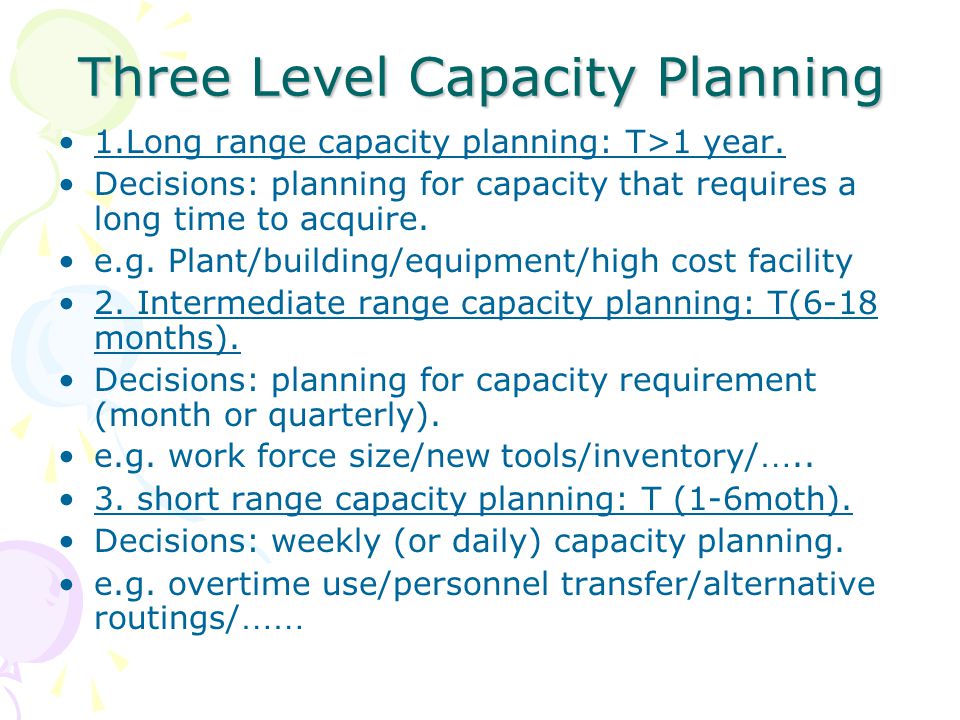



Long Rang Capacity Planning Ppt Download




Short Term Capacity Planning Big Bang




Checklist Capacity Plan It Process Wiki
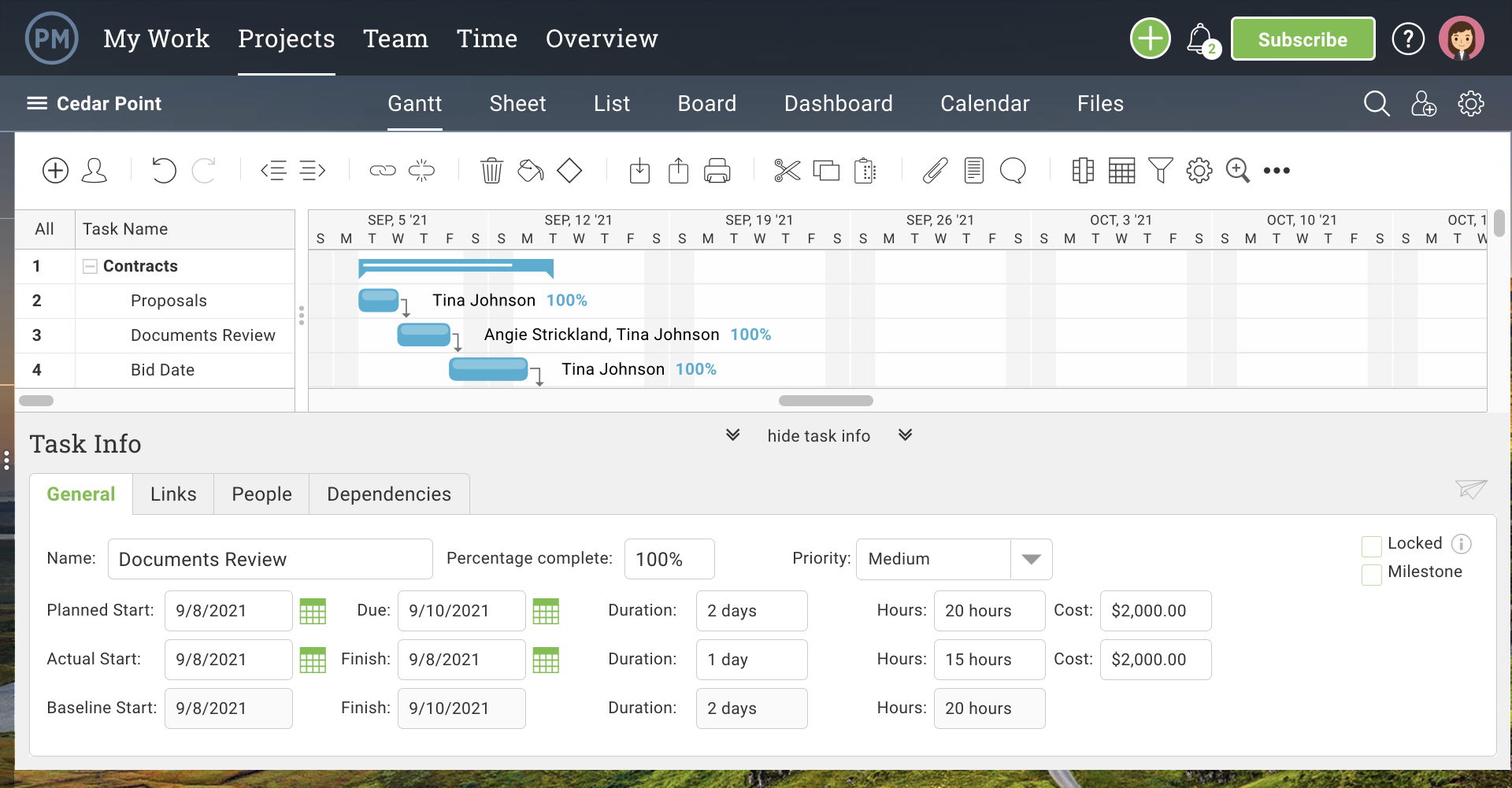



Capacity Planning What Is It And How Do I Implement It Projectmanager Com




Excel Based Resource Plan Template Free Download Project Management Templates
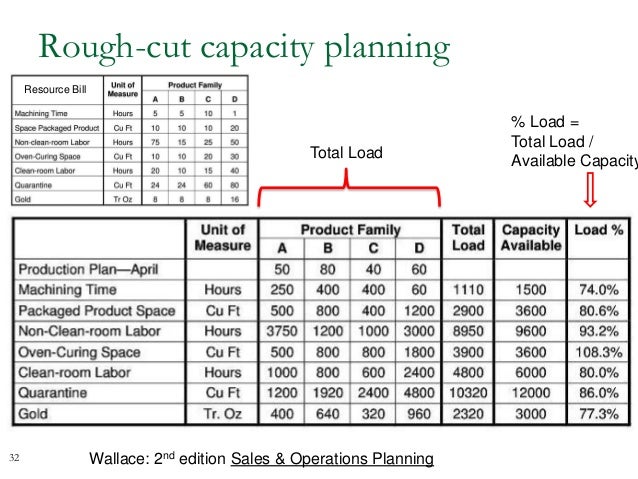



Klauuuudia Itil Capacity Plan Template




Level Capacity Plan Ppt Powerpoint Presentation Pictures Background Cpb Presentation Graphics Presentation Powerpoint Example Slide Templates
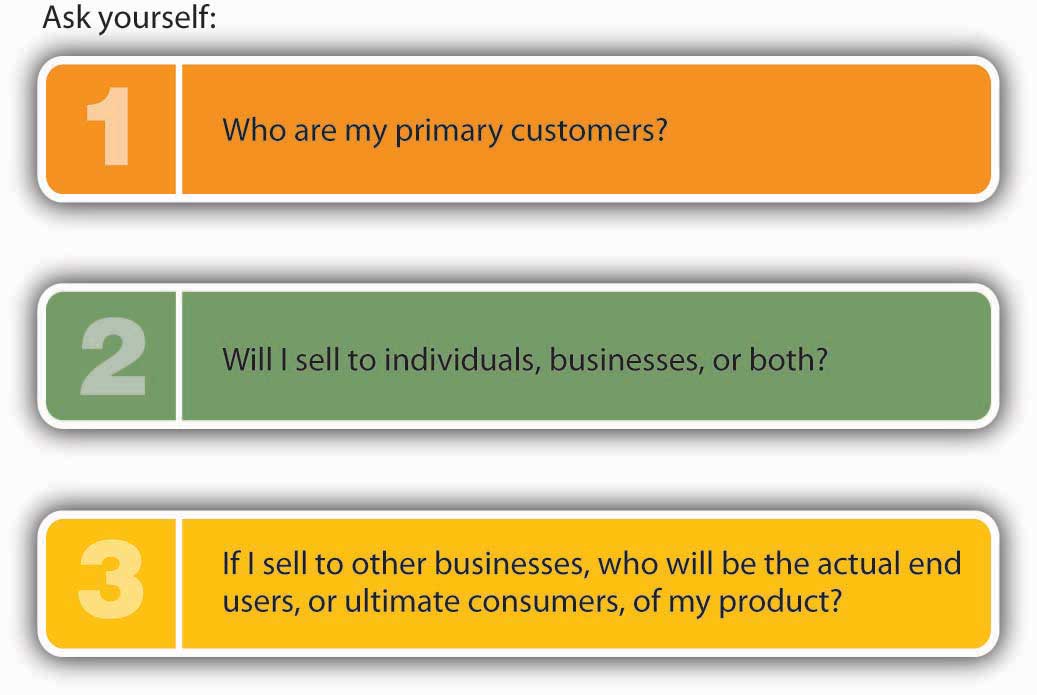



7 1 Capacity Planning Saylor Bus300 Operations Management
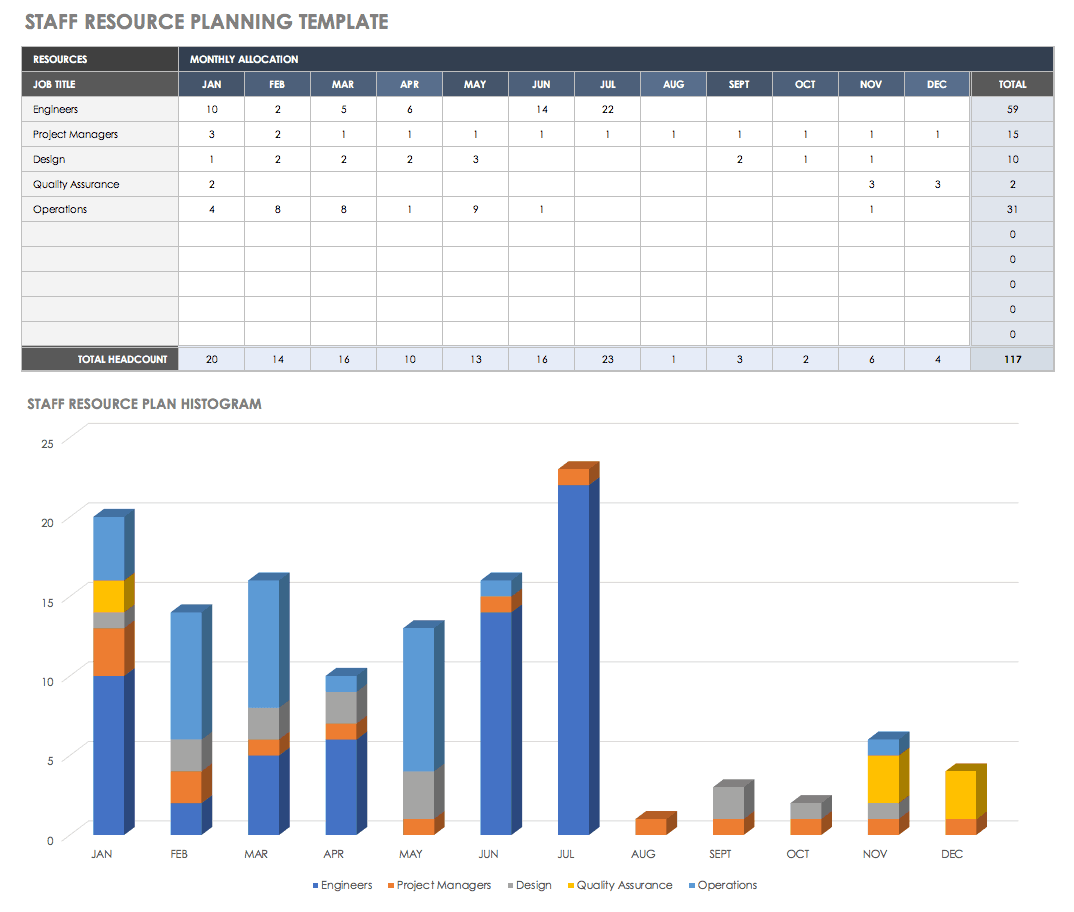



Free Resource Planning Templates Smartsheet




Capacity Planning Organization System Examples Definition System Long Term Capacity Planning
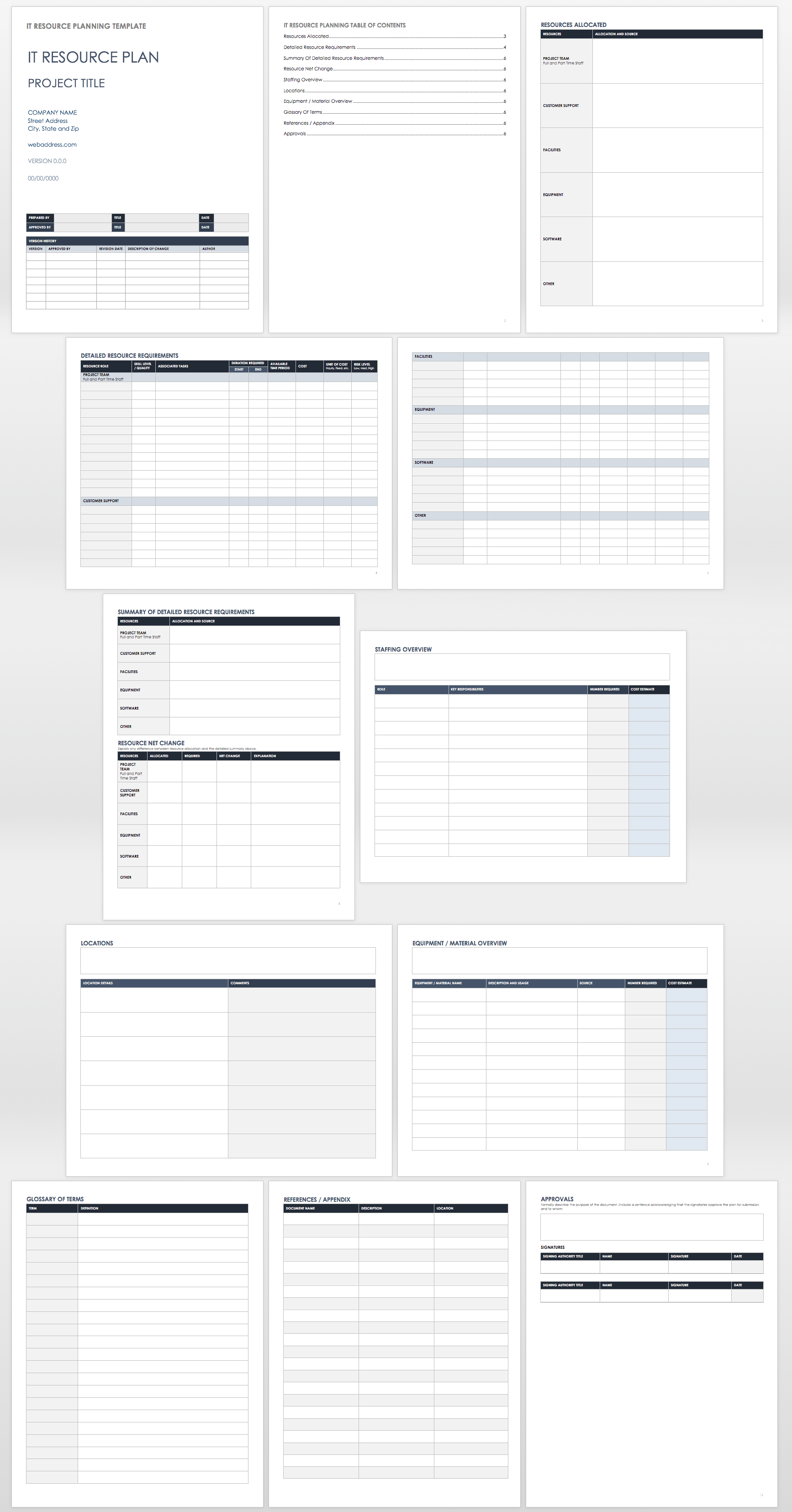



Free Resource Planning Templates Smartsheet




23 Capacity Planning Ideas Capacity Planning Capacity How To Plan




Metron Capacity Management Using Systems Capacity Data For Business Intelligence 3 Of 9




Production Planning Wikipedia
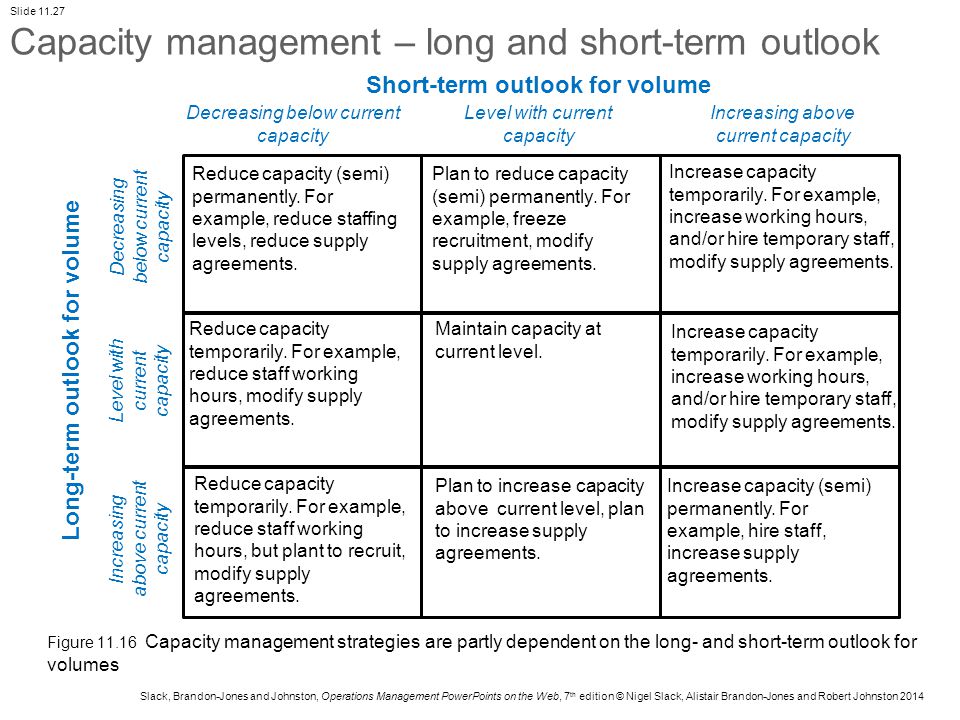



Chapter 11 Capacity Management Ppt Video Online Download




Capacity Planning Template Example Unique Capacity Plan Template Download Microsoft Word And Excel Capacity Planning Stem Lesson Plans Lesson Plan Templates




Capacity Planning Template Explore 7 Tips For Effective Planning Project Management Templates




Capacity Planning Template Explore 7 Tips For Effective Planning Project Management Templates




Metron Capacity Management Capacity Management Guided Practitioner Satnav Capacity Plan 16 Of 17




Capacity Planning Everything You Need To Know Clicktime
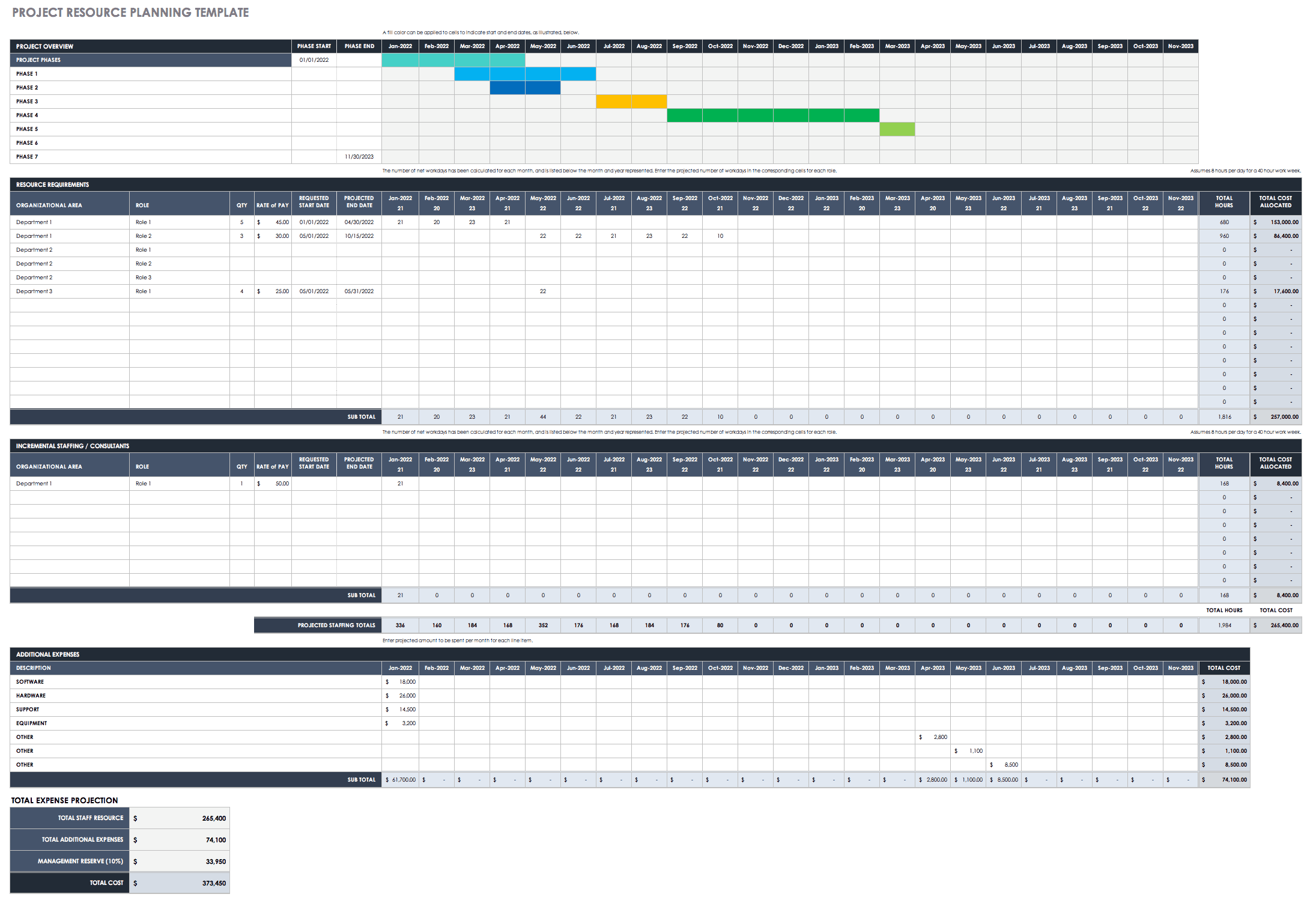



Free Resource Planning Templates Smartsheet




Capacity Planning 3 Methods How To Implement Them Optimoroute




A Critical Insight To Successful Supply Chain Planning




Capacity Planning In Project Management 4 Vital Success Factors Update 21




Capacity Planning Template Free Download
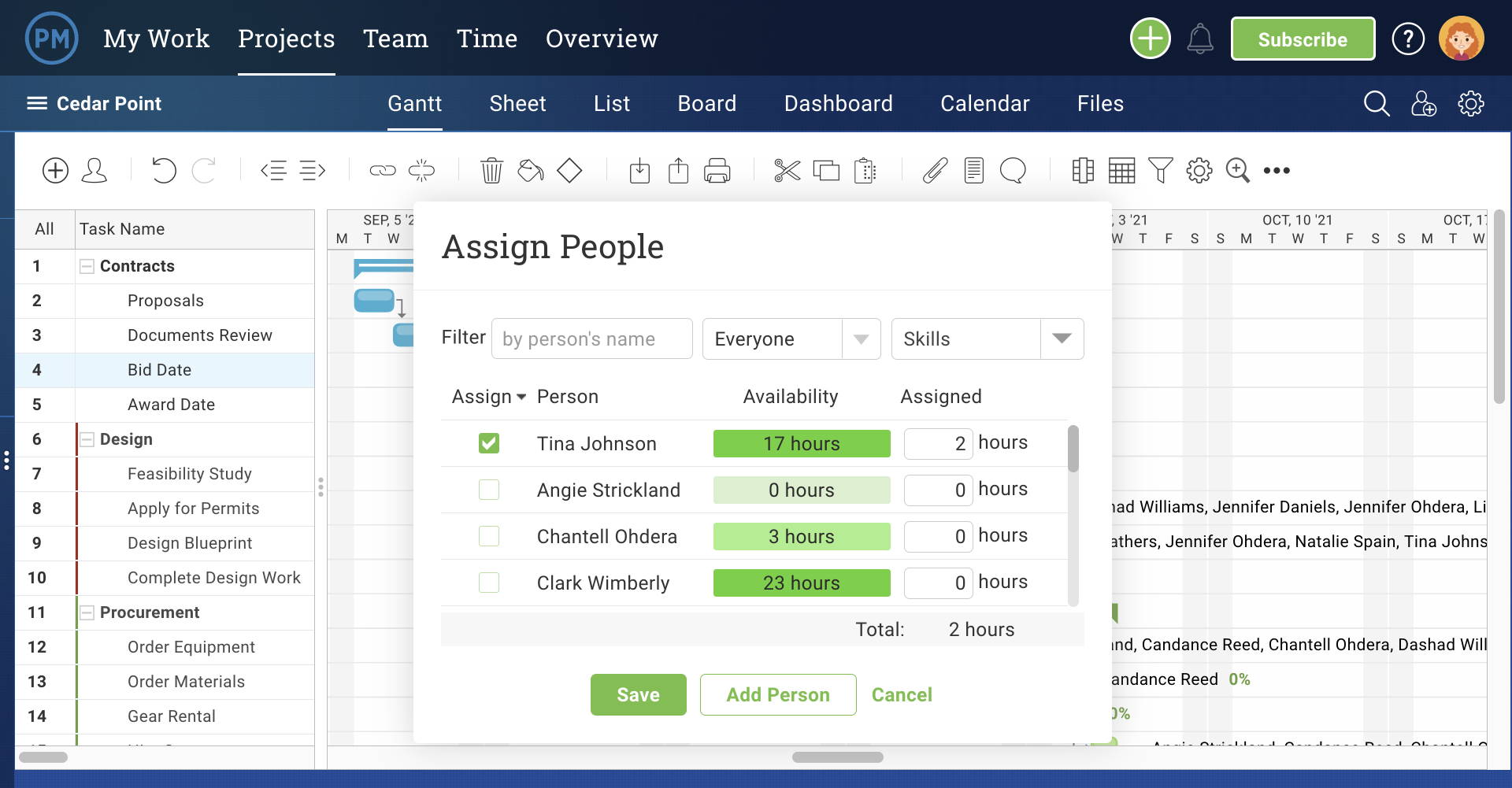



Capacity Planning What Is It And How Do I Implement It Projectmanager Com



Capacity Plan Template Technical Writing Tools




L D Capacity Planning Checklist 5 Steps To Effective Resource Management Synapse




Capacity Planning 3 Methods How To Implement Them Optimoroute
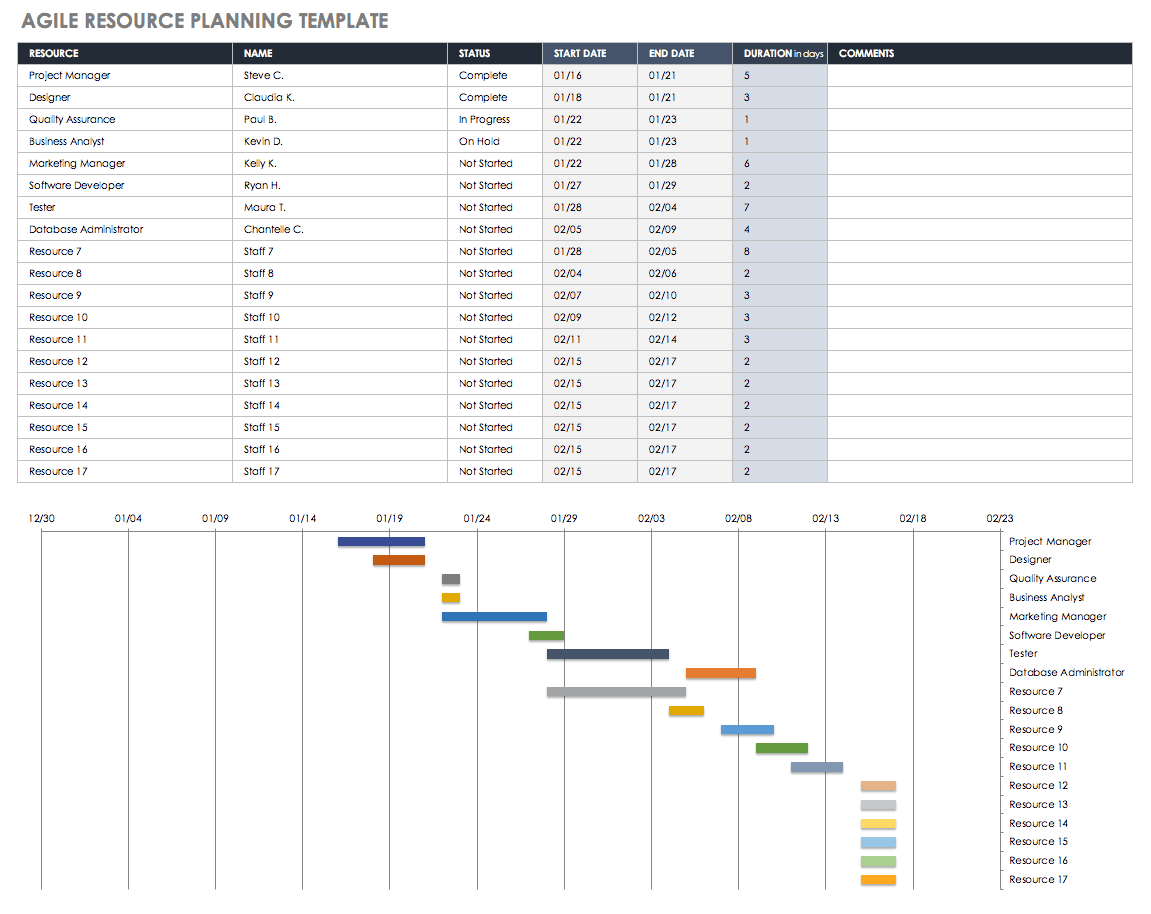



Free Resource Planning Templates Smartsheet
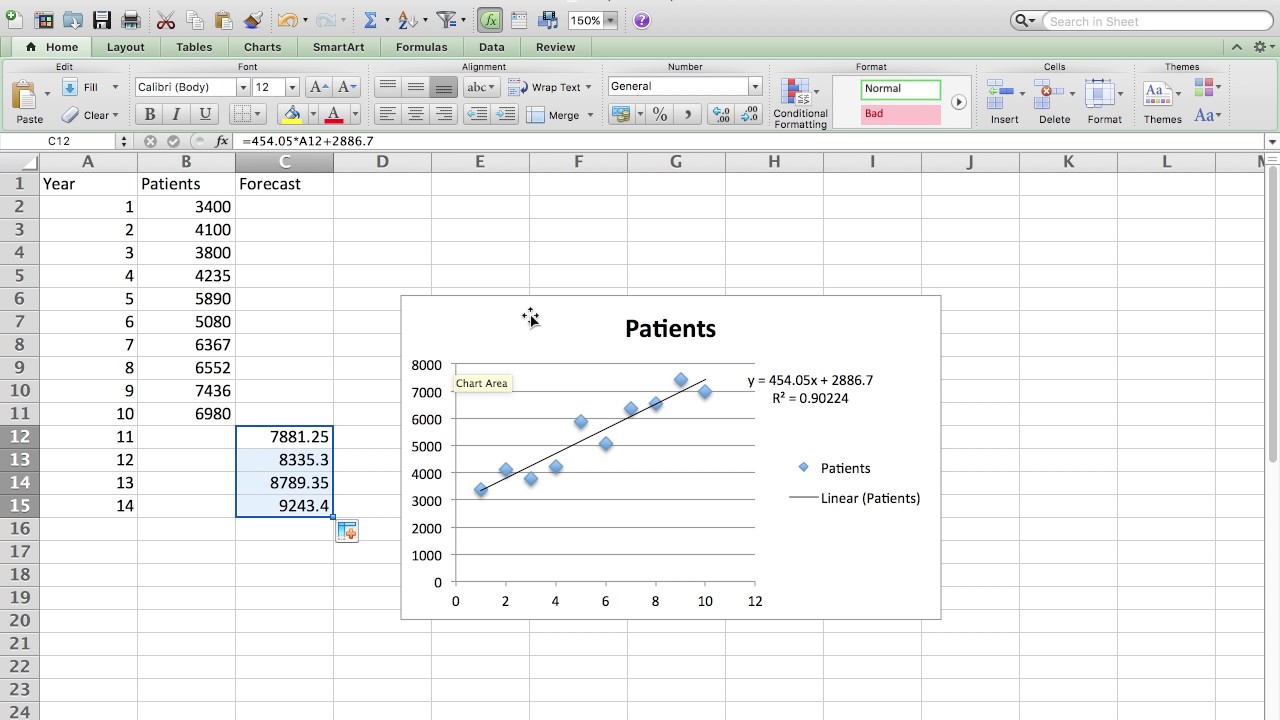



Capacity Planning Process Youtube




Capacity Planning Everything You Need To Know Clicktime
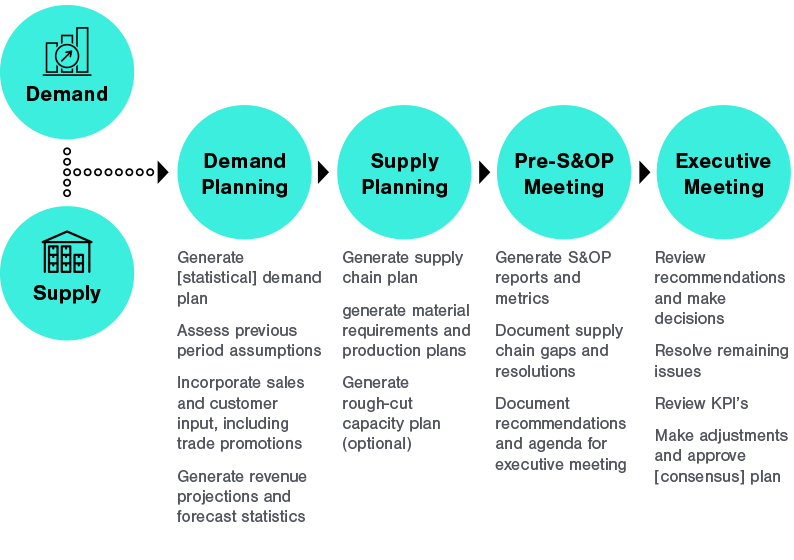



Implementing A Sales Operations Planning S Op Process Plex Demandcaster



Master Production Schedule
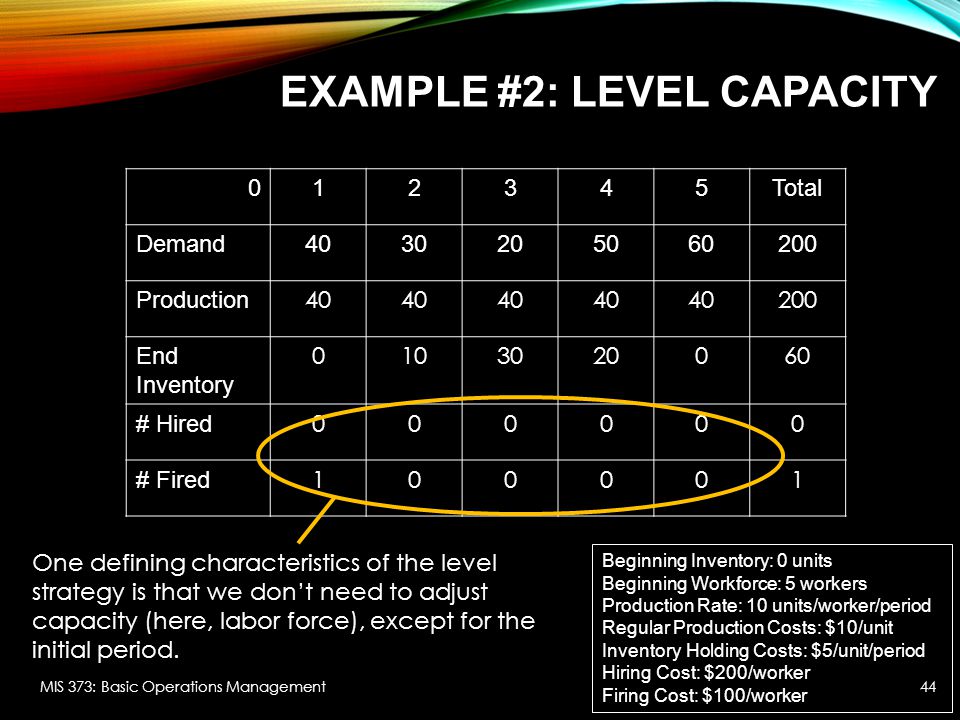



Aggregate Planning Chapter 11 Mis 373 Basic Operations Management Ppt Download




Resource Planning Template Excel Free Download



Uninote Ecommerce S3 Eu West 2 Amazonaws Com Capacity management Pdf




Capacity Plan Template Word Templates For Free Download




Checklist Capacity Plan It Process Wiki



Resource And Capacity Management




Capacity Planning 3 Methods How To Implement Them Optimoroute




The Itil Capacity Plan Is Used To Manage The Resources Required To Deliver It Services Capacity Planning How To Plan Templates
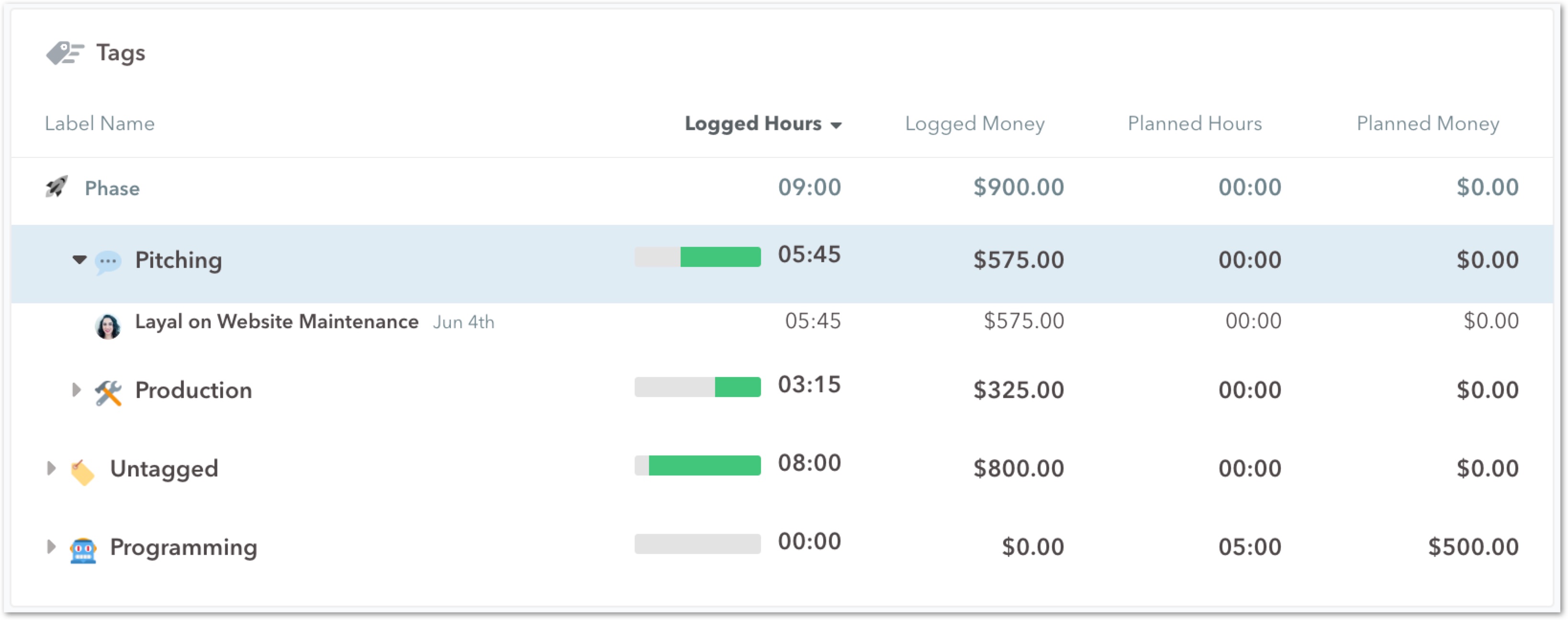



Capacity Planning What It Is How To Do It Well




Capacity Planning What Is It And How Do I Implement It Projectmanager Com



3




Level Capacity Plan Ppt Powerpoint Presentation Pictures Background Cpb Presentation Graphics Presentation Powerpoint Example Slide Templates




How Is Yield Management Implemented In Airline Industry Ayat Saleh




5 Steps To Create A Tech Support Capacity Plan The Operations Blog
0 件のコメント:
コメントを投稿